June 8, 2024
What Is Lean And Why Its A Concern
Discover the power of Lean principles and implementation strategies.
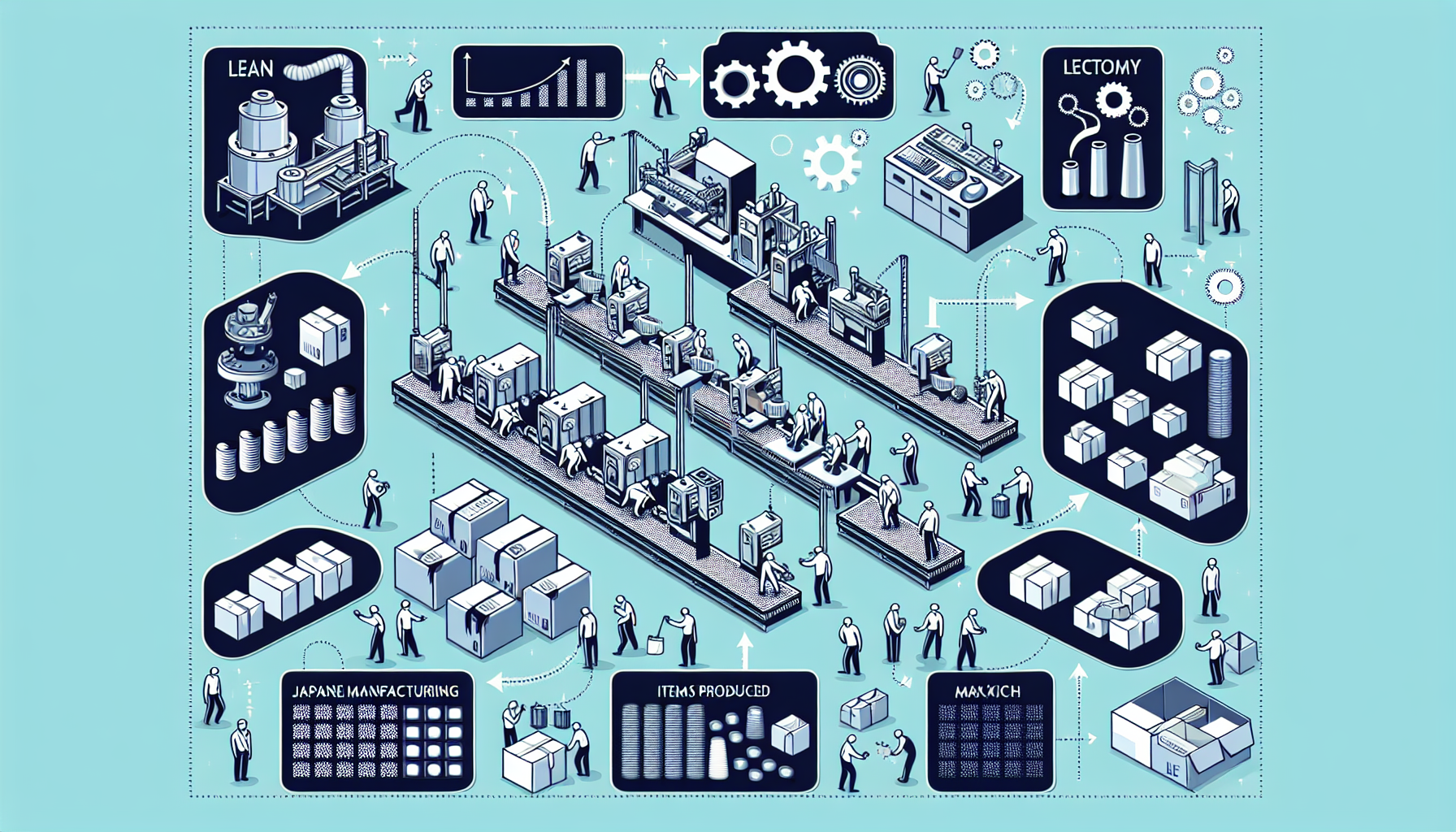
Introduction to Lean
When it comes to improving processes and increasing efficiency, Lean is a methodology that has gained significant popularity across industries. In this section, we will explore the basic concepts of Lean and its origins.
What is Lean?
At its core, Lean is a systematic approach that focuses on eliminating waste and maximizing value. It aims to create more value for customers while minimizing resources and efforts that do not add value. Lean principles emphasize continuous improvement, teamwork, and the involvement of every individual within an organization.
Lean originated from the Toyota Production System (TPS), which was developed by Toyota in the 1940s. The TPS revolutionized manufacturing by introducing concepts such as just-in-time production and autonomation (automation with a human touch). Over time, the principles and practices of Lean spread beyond the manufacturing sector and are now widely adopted in various industries, including healthcare, services, and software development.
Origins of Lean Culture
The roots of Lean culture can be traced back to the Japanese philosophy of Kaizen, which means continuous improvement. Kaizen emphasizes the importance of small, incremental changes that lead to significant improvements over time. It encourages employees at all levels of an organization to identify problems, suggest improvements, and take part in the decision-making process.
Another influential concept in Lean culture is Gemba, which means "the real place" or "where the action happens." It involves going to the actual workplace to observe and understand the processes, gather data, and identify opportunities for improvement. By engaging directly with the work environment, organizations can make informed decisions and implement changes that have a direct impact on productivity and quality.
Lean culture also promotes the idea of respect for people. This involves nurturing a collaborative and supportive work environment where every individual is empowered to contribute their ideas and expertise. By valuing the input of employees and fostering a culture of continuous learning, organizations can create a strong foundation for Lean implementation.
Understanding the basic principles and origins of Lean is essential for organizations and individuals looking to embrace Lean methodologies. By adopting Lean principles, organizations can optimize their processes, reduce waste, and enhance overall efficiency to deliver greater value to their customers.
Why Lean Matters
Understanding the importance of lean principles and the benefits of implementing lean practices is essential for organizations seeking to improve efficiency and reduce waste. Let's explore why lean matters in various industries.
Importance of Lean Principles
Lean principles provide a framework for organizations to streamline their processes, eliminate waste, and deliver value to customers. By embracing lean principles, organizations can achieve the following:
- Improved Efficiency: Lean principles focus on optimizing processes and eliminating non-value-added activities. This leads to increased productivity, reduced lead times, and improved overall efficiency.
- Enhanced Quality: Lean principles emphasize the importance of consistently delivering high-quality products or services. By identifying and eliminating defects and errors through continuous improvement, organizations can enhance customer satisfaction and loyalty.
- Increased Flexibility: Lean principles enable organizations to respond quickly to changing market demands. By eliminating bottlenecks, reducing setup times, and implementing flexible manufacturing systems, organizations can adapt to customer needs more effectively.
- Empowered Workforce: Lean principles encourage employee engagement and empowerment. By involving employees in process improvement initiatives, organizations can tap into their expertise and creativity, leading to higher job satisfaction and increased morale.
Benefits of Implementing Lean
Implementing lean practices can yield numerous benefits for organizations, including:
- Reduced Waste: Lean methodologies focus on identifying and eliminating waste in processes, such as overproduction, waiting time, inventory excess, and unnecessary transportation. This reduction in waste leads to cost savings and improved resource utilization.
- Improved Customer Satisfaction: Lean practices aim to deliver value to customers by focusing on their needs and expectations. By reducing lead times, improving product quality, and enhancing responsiveness, organizations can enhance customer satisfaction and loyalty.
- Cost Savings: As lean practices eliminate waste and optimize processes, organizations can achieve cost savings through reduced inventory holding costs, improved resource allocation, and minimized rework or scrap.
- Increased Profitability: By improving efficiency, reducing waste, and enhancing customer satisfaction, organizations can achieve greater profitability. Lean practices contribute to higher revenues, lower costs, and improved financial performance.
- Competitive Advantage: Organizations that implement lean practices gain a competitive edge in the market. The ability to deliver high-quality products or services quickly and efficiently sets them apart from competitors and positions them as leaders in their industry.
The importance of lean principles and the benefits of implementing lean practices cannot be overstated. By embracing lean methodologies, organizations can achieve operational excellence, enhance customer satisfaction, and drive long-term success.
Key Concepts of Lean
To fully understand Lean principles and its application, it's important to grasp the key concepts that form its foundation. These concepts include value, value stream, flow, pull, and continuous improvement.
Value
In Lean, value refers to anything that the customer is willing to pay for. It can be a product feature, a service, or any aspect that enhances the customer experience. Identifying and understanding what creates value for the customer is essential in eliminating waste and optimizing processes.
Value Stream
A value stream represents the entire set of activities required to deliver a specific product or service. It encompasses all the steps and processes involved, from the raw materials to the final product or service reaching the customer. Analyzing and mapping the value stream helps identify areas of waste and inefficiency, enabling organizations to streamline their processes.
Flow
Flow is the smooth and uninterrupted movement of products, services, and information through the value stream. By eliminating bottlenecks, delays, and unnecessary steps, organizations can achieve a continuous flow that minimizes waste and maximizes efficiency. Implementing strategies like visual management, standardizing work processes, and optimizing layouts can help achieve a more seamless flow.
Pull
Pull is a concept that emphasizes producing only what is needed, when it is needed, and in the quantity required by the downstream process or customer. Instead of pushing products or services through the value stream based on forecasts or assumptions, the pull system relies on actual demand. This approach helps avoid overproduction and reduces inventory, leading to cost savings and improved responsiveness.
Continuous Improvement
Continuous improvement, also known as Kaizen, is a fundamental aspect of Lean. It involves a systematic approach to identifying and eliminating waste, improving processes, and driving innovation. Through the consistent application of small incremental changes, organizations can achieve significant improvements over time. Continuous improvement fosters a culture of learning, collaboration, and adaptability, enabling organizations to stay competitive and meet changing customer needs.
By understanding and embracing these key concepts of Lean, organizations can transform their operations, improve efficiency, and deliver value to their customers. Each concept plays a vital role in creating a Lean culture and driving continuous improvement.
Lean Tools and Techniques
To effectively implement lean principles and improve efficiency, organizations utilize various tools and techniques. Let's explore four commonly used lean tools and techniques: 5S, Kanban, Kaizen, and Just-in-Time (JIT).
5S
5S is a systematic approach to workplace organization that focuses on creating a clean, organized, and efficient work environment. The five steps of 5S are:
- Sort (Seiri): Eliminate unnecessary items and organize the workplace by separating essential items from non-essential ones.
- Set in Order (Seiton): Arrange the remaining items in a logical and organized manner to enhance accessibility and productivity.
- Shine (Seiso): Regularly clean and maintain the workplace to promote a safe and efficient working environment.
- Standardize (Seiketsu): Establish standardized procedures and visual controls to ensure consistency and reduce errors.
- Sustain (Shitsuke): Continuously maintain and improve the 5S practices to sustain the benefits over time.
Implementing 5S principles helps reduce waste, improve safety, and promote a more productive and organized work environment.
Kanban
Kanban is a visual system used to manage and control the flow of work. It provides a clear and transparent view of the work process, allowing teams to identify and address bottlenecks and improve overall workflow. Key components of Kanban include:
- Kanban Board: A visual representation of the work process, divided into columns representing different stages of the workflow.
- Cards or Post-Its: Each task or work item is represented by a card or post-it note placed on the Kanban board, indicating its status and progress.
- Work-in-Progress (WIP) Limits: Setting limits on the number of tasks allowed in each column helps prevent overloading and promotes smooth flow.
By visualizing the work and limiting work-in-progress, Kanban enables teams to optimize their workflow, increase efficiency, and deliver value more effectively.
Kaizen
Kaizen, a Japanese term meaning "continuous improvement," is a philosophy and methodology that focuses on making incremental and continuous improvements in all aspects of an organization. It emphasizes the involvement of employees at all levels to identify and implement small, positive changes over time.
Key elements of Kaizen include:
- Gemba Walks: Engaging employees to observe and gather insights from the actual workplace to identify improvement opportunities.
- PDCA (Plan-Do-Check-Act) Cycle: A four-step iterative process for problem-solving and decision-making to drive continuous improvement.
- Employee Involvement: Encouraging and empowering employees to contribute their ideas and suggestions for improvement.
Kaizen fosters a culture of continuous learning, innovation, and improvement, leading to increased efficiency, quality, and employee engagement.
Just-in-Time (JIT)
Just-in-Time (JIT) is a production strategy that aims to produce and deliver goods or services at the exact moment they are needed, thereby minimizing waste and reducing inventory levels. Key principles of JIT include:
- Demand-driven Production: Producing items based on customer demand, reducing the need for excessive inventory.
- Pull System: Replenishing materials and resources based on actual customer orders or consumption, rather than forecasts or speculation.
- Quick Changeover: Streamlining changeover processes to minimize downtime and enable flexible production in response to changing customer needs.
By adopting JIT principles, organizations can reduce waste, improve efficiency, and enhance customer satisfaction by delivering products or services in a timely and cost-effective manner.
These lean tools and techniques provide organizations with practical solutions to improve their processes, optimize workflow, and ultimately enhance overall productivity and customer value.
Lean in Practice
Implementing lean principles in real-world scenarios has proven to be effective in improving efficiency, reducing waste, and enhancing overall productivity. Let's explore some real-world examples of lean implementation and success stories of lean transformation.
Real-world Examples of Lean Implementation
Example 1: Toyota Production System
One of the most well-known examples of lean implementation is the Toyota Production System (TPS). Developed by Toyota, this system revolutionized the manufacturing industry. TPS focuses on eliminating waste and continuously improving processes to deliver high-quality products efficiently.
By implementing lean principles such as just-in-time (JIT) production, where materials are delivered as needed, and kanban systems, which optimize inventory management, Toyota significantly reduced waste, improved productivity, and enhanced customer satisfaction. The success of TPS has inspired many other organizations to adopt lean practices.
Example 2: Lean Healthcare
Lean principles have also been successfully applied in the healthcare industry. Hospitals and healthcare facilities have implemented lean methodologies to streamline processes, reduce waiting times, and enhance patient care.
For instance, Virginia Mason Medical Center in Seattle, Washington, embarked on a lean transformation journey to improve patient safety and quality of care. By implementing lean practices such as value stream mapping, 5S methodology for workplace organization, and continuous improvement through kaizen events, they were able to reduce medication errors, decrease patient wait times, and improve overall patient satisfaction.
Success Stories of Lean Transformation
Success Story 1: General Electric (GE)
General Electric (GE) is a prime example of a company that successfully transformed its operations using lean principles. GE adopted the lean methodology known as "Work-Out," which encourages employee involvement and collaboration to identify and solve problems.
By implementing lean practices across various departments and business units, GE achieved significant improvements in efficiency, cost reduction, and customer satisfaction. The company's lean transformation resulted in streamlined processes, reduced lead times, and increased productivity, ultimately driving their success in the competitive market.
Success Story 2: Amazon
Amazon, the e-commerce giant, has embraced lean principles throughout its operations. The company continuously strives to eliminate waste, optimize logistics, and enhance customer experience. Amazon's fulfillment centers utilize lean strategies such as efficient inventory management, automated processes, and data-driven decision-making to deliver products to customers quickly and accurately.
By applying lean methodologies, Amazon has been able to achieve remarkable success in terms of customer satisfaction, rapid order fulfillment, and operational efficiency. Their lean practices have contributed to their position as a leader in the e-commerce industry.
These real-world examples and success stories demonstrate the effectiveness of lean implementation across different industries. By adopting lean principles and methodologies, organizations can streamline their processes, eliminate waste, and drive continuous improvement, leading to enhanced productivity, customer satisfaction, and overall success.
Overcoming Challenges with Lean
Implementing lean principles and practices can bring about significant improvements in efficiency and productivity. However, like any change initiative, there are common obstacles that organizations may encounter during the lean implementation process. In this section, we will discuss some of these common obstacles and provide strategies for overcoming them.
Common Obstacles in Lean Implementation
Strategies for Overcoming Lean Challenges
To overcome the common obstacles encountered during lean implementation, organizations can employ several strategies:
- Develop Leadership Support: It is crucial to secure leadership support and involvement from the outset. Leaders should champion the lean initiatives, communicate their importance, and actively participate in the implementation process. This helps to create a culture of continuous improvement and motivates employees to embrace the changes.
- Promote Change Management: Addressing resistance to change requires effective change management strategies. Organizations should engage employees in the change process, provide clear communication about the purpose and benefits of lean, and offer training and support to help employees adapt to new roles and responsibilities.
- Invest in Training and Education: Providing comprehensive training and education on lean principles and tools is essential for successful implementation. This can include workshops, seminars, and on-the-job training to ensure that employees have the necessary knowledge and skills to actively participate in lean initiatives.
- Encourage Continuous Learning and Improvement: Lean is not a one-time implementation; it is an ongoing journey of continuous improvement. Organizations should foster a culture of learning and improvement, encouraging employees to share ideas, experiment with new approaches, and continuously seek ways to eliminate waste and enhance efficiency.
By recognizing and addressing these common obstacles, organizations can enhance the chances of successful lean implementation. Overcoming these challenges requires a commitment to leadership support, change management, training, and a culture of continuous improvement. With perseverance and a focus on overcoming obstacles, organizations can reap the full benefits of lean principles and practices.